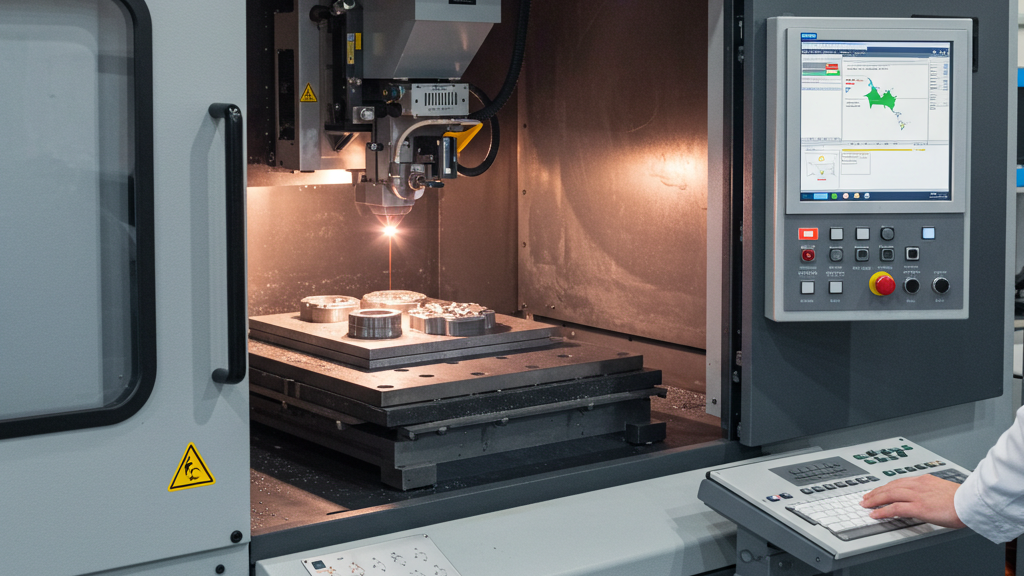
Metal 3D printing, as a key technology in advanced manufacturing, is leading industrial transformation. It directly manufactures complex parts by layer-by-layer deposition of metal materials, breaking through the limitations of traditional manufacturing. This technology is widely used in aerospace, medical and other fields, and exhibits great potential for customization and rapid manufacturing. Understanding its core principles is key to grasping the future development of this technology.
The previous text introduced the importance of metal 3D printing and its applications. Precise control of metal melting and solidification is the core to achieving high-quality printing. Different printing technologies, such as Selective Laser Melting (SLM) and Electron Beam Melting (EBM), are based on different energy sources and material delivery methods. Next, we will focus on introducing the working principles and unique advantages of several mainstream metal 3D printing technologies.
How to go from model to solid?
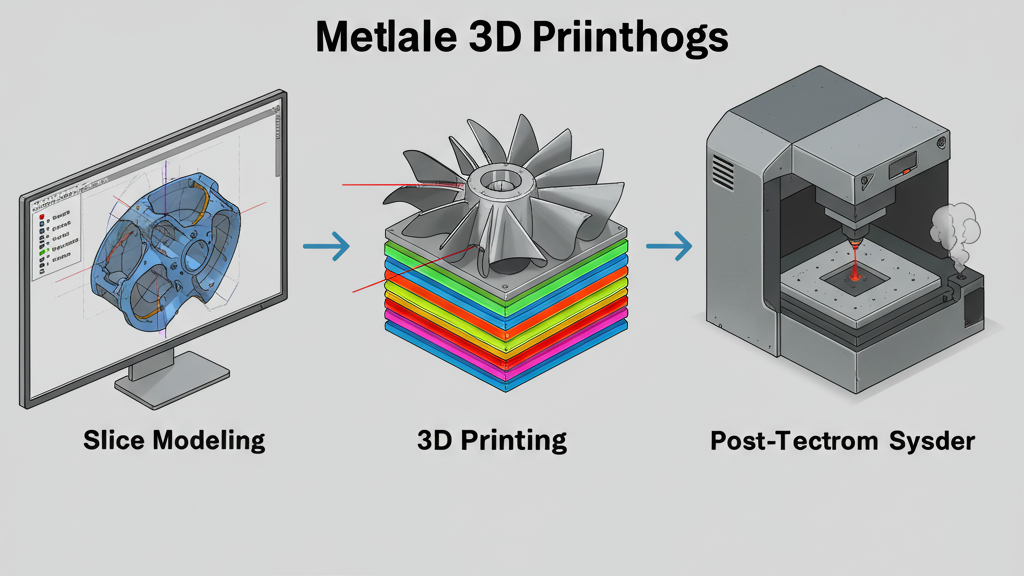
The primary step in metal 3D printing is to transform the digital blueprint into manufacturable instructions, which lays the foundation for the subsequent physical construction. From a Computer-Aided Design (CAD) model to the final metal part, a series of precise digital processing and path planning is involved.
- Digital Model Preparation and Slicing: Through CAD modeling and slicing software, the digital model is converted into layer-by-layer path data that the printer can execute.
- Material Melting and Deposition: A high-energy beam or binder selectively melts, sinters, or bonds the metal material to form a single-layer structure.
- Layer-by-Layer Construction: The powder spreading and melting/bonding processes are repeated to build up a three-dimensional solid part layer by layer.
- Post-Processing: The printed parts need to undergo processes such as cleaning, heat treatment, and surface treatment to meet performance and accuracy requirements.
How is metal melted/bonded into shape?
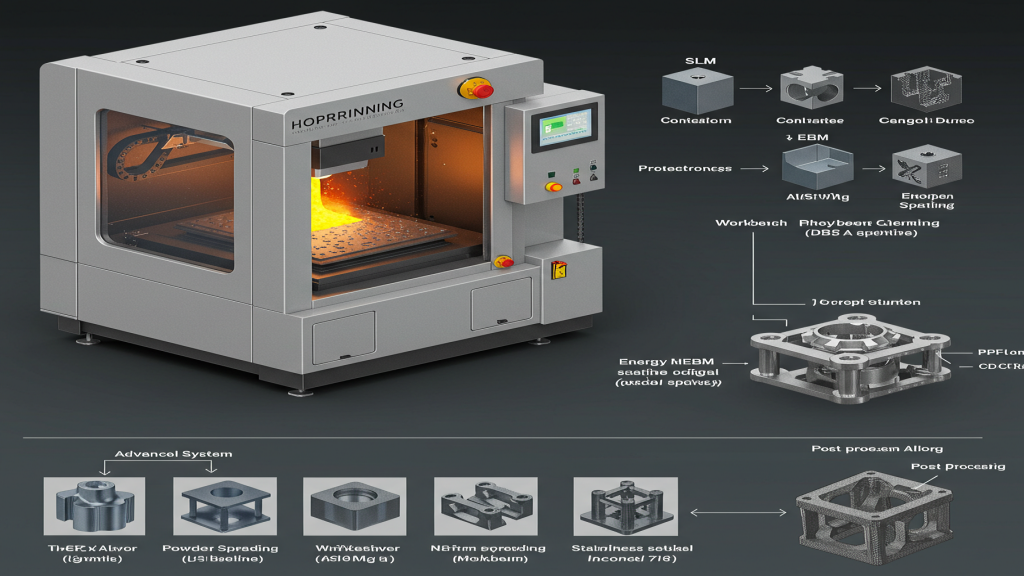
The key to metal 3D printing lies in the precise energy input or binder application to the metal material to achieve a strong bond between layers. In the layer-by-layer manufacturing process, whether it is high-temperature melting or chemical bonding, the core objective is to ensure that the newly deposited material forms an effective metallurgical or physical connection with the layer below, thereby constructing a three-dimensional structure with sufficient strength.
- Energy Beam Melting and Metallurgical Bonding: A high-energy beam melts the metal powder and metallurgically bonds it with the underlying layer to form a dense structure.
- Binder Jetting and Subsequent Sintering: A binder bonds the powder, and then sintering is performed to achieve metallurgical bonding between the metal particles.
- Remelting and Interdiffusion of Molten Layers: Remelting and atomic diffusion between new and old layers enhance the interlayer bonding strength.
- Precise Control of Process Parameters: Precise control of printing parameters is a key guarantee for forming a stable structure.
Differences in Technological Principles?
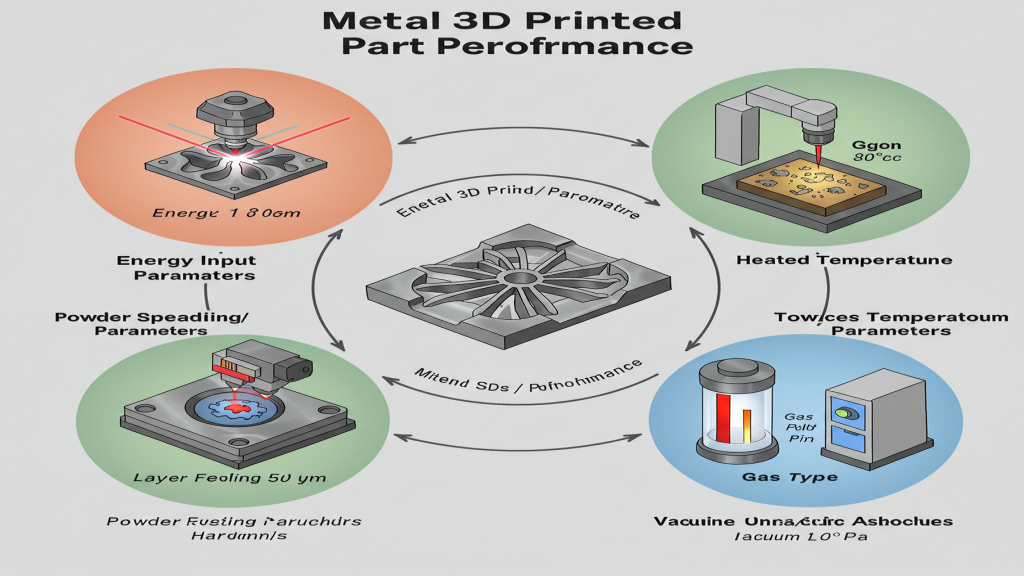
Although both are additive manufacturing, different metal 3D printing technologies exhibit significant differences in energy sources, material delivery methods, and forming mechanisms. Understanding the essential differences between technologies such as Selective Laser Melting (SLM) and Electron Beam Melting (EBM) helps in selecting the most suitable manufacturing solution for specific application scenarios.
- Energy Source and Action Mode: Different technologies use different methods such as lasers, electron beams, or binders to act on metal materials.
- Material Form and Delivery Method: Powder materials are mainly used, but the powder spreading and feeding methods are different. Some technologies also use wire materials.
- Working Environment and Atmosphere Control: Different technologies have specific requirements for the working environment and atmosphere, such as protective gas or vacuum.
- Forming Accuracy and Material Properties: Energy sources and process characteristics cause differences in accuracy, surface quality, and mechanical properties among various technologies.
Comparative Analysis of Core Principles of Different 3D Printing Technologies
Feature |
SLM (Selective Laser Melting) |
EBM (Electron Beam Melting) |
Binder Jetting |
DED (Directed Energy Deposition) |
Energy Source | Laser Beam | Electron Beam | Binder | Laser/Electron Beam |
Working Principle | Melts Powder | Melts Powder | Bonds Powder, then Sintered | Melts Fed Powder/Wire |
Environment | Protective Gas | Vacuum | Regular | Protective Gas |
Key Advantages | High Precision | Fast Speed, Low Stress | Low Cost, Wide Material Range | Repair Capable, Multi-Material |
Key Disadvantages | Slow Speed, High Cost | Rough Surface | Requires Sintering, Limited Precision | Lower Precision |
Key Factors Affecting Part Performance
The core process parameters that affect the final performance of metal 3D printed parts are numerous and interrelated, playing a crucial role in key indicators such as strength and accuracy. Precisely controlling parameters such as the power and scanning speed of the laser or electron beam, powder bed temperature, layer thickness, powder feeding rate, and protective atmosphere can directly affect the melting quality, solidification behavior, and microstructure of the metal.
1.Energy Input Parameters: Power and speed directly determine the metal melting quality and part performance.
2.Powder Spreading/Feeding Parameters: Layer thickness, uniformity, and powder feeding rate affect part accuracy and material deposition.
3.Temperature Control Parameters: Preheating and process temperature are essential for reducing stress, improving bonding, and preventing deformation.
4.Environment and Atmosphere Parameters: Gas type, purity, and vacuum level directly affect the chemical composition and mechanical properties of the material.
Conclusion
Metal 3D printing technology transforms digital models into layer-by-layer built physical entities, enabling the fabrication of complex geometries. Its core principle lies in precisely controlling the interaction between the energy source and the metal material, whether through high-energy beam melting, binder jetting, or direct material deposition, the goal is to construct a stable three-dimensional structure with the desired properties.
For expert assistance in implementing for your production needs, visit our resource center or contact us. Let’s help you scale up your manufacturing with precision and efficiency!
Post time: Apr-22-2025